Tackling Plastic with Juniper Networks & Aston Martin Aramco F1®: Packaging, Models, and Beyond
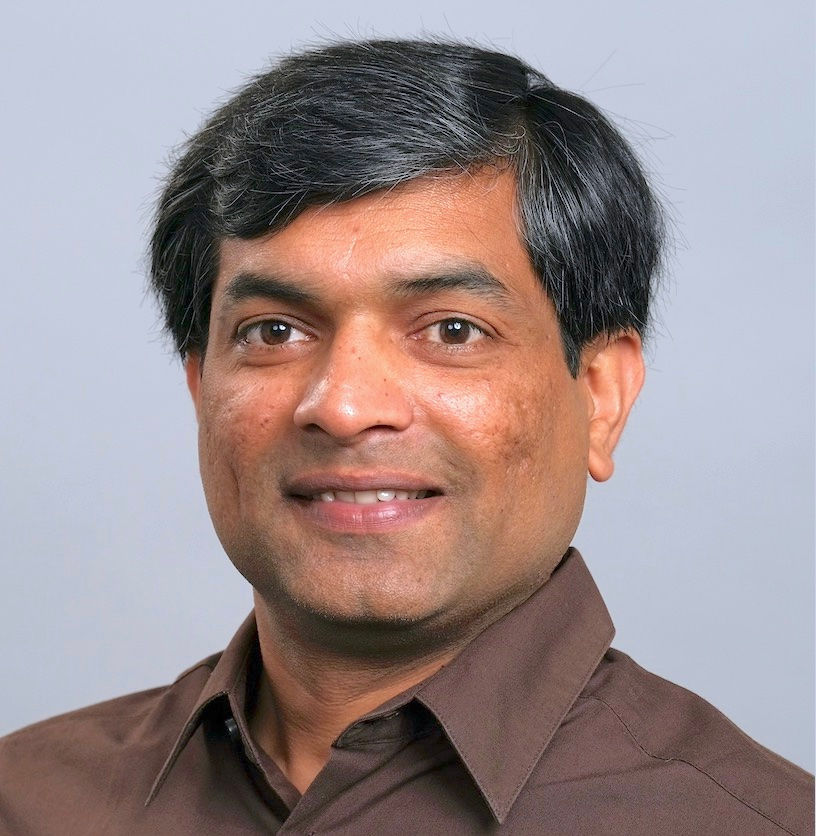
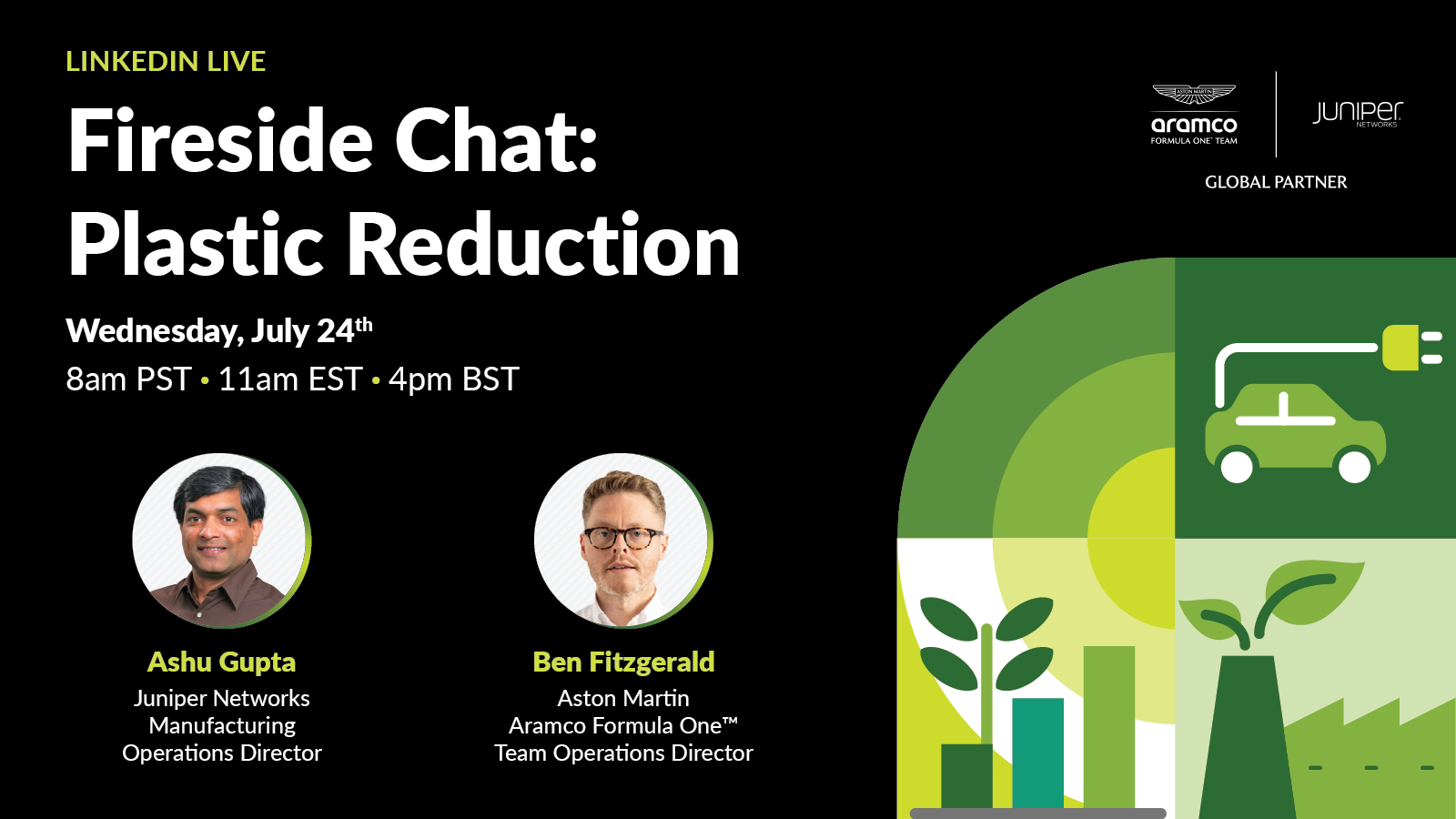
Tackling Plastic in Formula One: Packaging, Models, and Beyond
Plastic waste is a huge roadblock to enterprise sustainability goals. Taking the first step to tackling your enterprises’ plastic use is much easier when you learn about the successful tactics others are using. In this video, Juniper and Aston Martin Aramco F1® Team sit down for a fireside chat to discuss the team’s initiatives to reduce plastic in their operations.
You’ll learn
About the difficulties and successes of implementing plastic reduction strategies, including overcoming resistance, finding alternatives, collaborating with stakeholders, and measuring impact
How the team balances its need to win on the weekends with its consumption of plastics
What it takes to drive down plastic consumption in your own organization
Who is this for?
Host
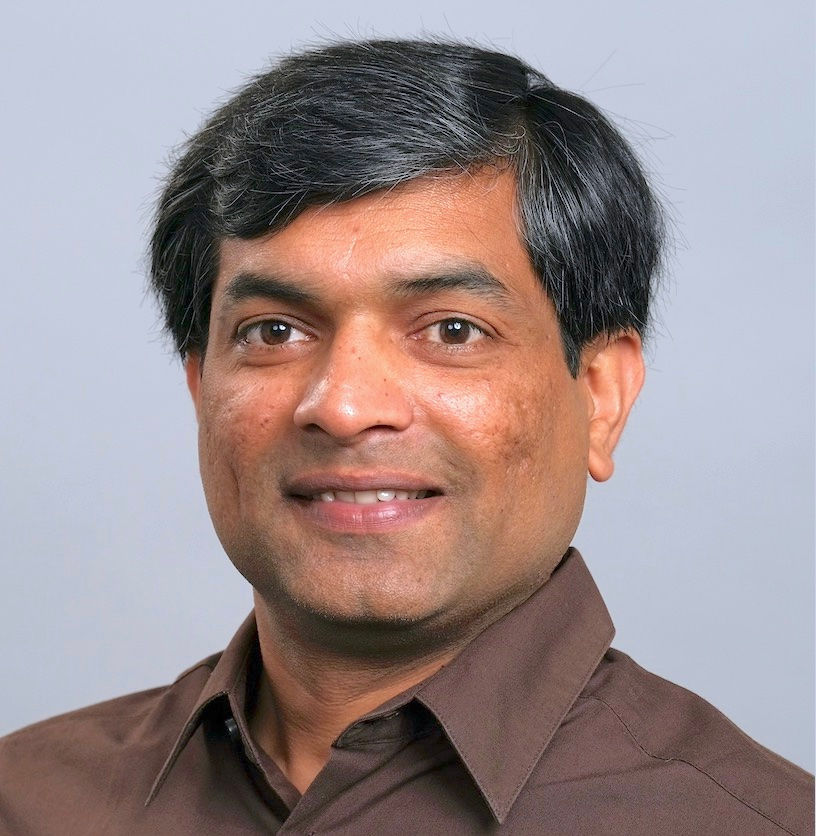
Guest speakers
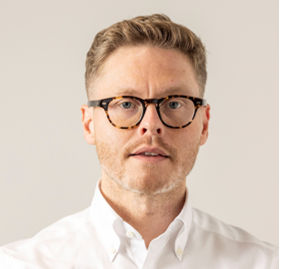
Experience More
Transcript
0:02 hello everyone welcome to today's fireside chat on waste reduction especially
0:10 plastic waste I am Ashu Gupta uh director for manufacturing operations in
0:16 Juniper and today I have the distinct pleasure of inviting uh Our Guest Ben
0:23 fitgerald who is the director of operations for eston Martin aramco Formula 1 team welcome Ben hi Ashley
0:32 thank you thank you to everybody for inviting me so before we get started Ben
0:37 um can I just ask you to maybe give me a little bit of an introduction of what you do um in
0:44 amf1 yeah absolutely we've just heard from CLA uh our Chief Information
0:49 officer and um and Eric our Deputy technical director both of those people obviously work within uh the team here
0:56 at silverston to continue to develop race after race year after year our
1:01 Formula 1 car um and fundamentally my responsibility at the at the simplest level is to make sure that the parts and
1:08 the product that is required to race are available track side and uh just for
1:14 everybody's benefit I explained to Ashu earlier today that um to get us to where
1:19 we are at this point in the season we've made nearly 10,000 parts per race so
1:24 what appears to be a very glamorous um race spectacle that we see on the
1:30 television um which ab absolutely is as a sport back at the factory there's a
1:35 huge effort all 850 staff we have here in silverston we work 24 hours a day
1:42 seven days a week to be able to get through the development of the car race after race week after week and in effect
1:50 we get to a point where um we have to do this in a sustainable um very uh
1:58 financially sound way and that drives our approach and Innovation on both
2:03 waste sustainability and um and value for money wonderful so so Ben before we get
2:11 started um I thought you know I was reading about the topic itself and there
2:17 were some amazing facts that I found related to plastic pollution so um I
2:23 want to talk to you about those uh before we get into the actual discussion so any
2:30 we generate about 400 million tons of plastic waste as species that's you know
2:39 I couldn't get my head around it so if I think about the total weight of humans
2:45 on this Earth we generate the equivalent of that in annual plastic waste every
2:51 year and only about 9% less than 10% of that gets recycled so if if you think
2:59 about that we are releasing into the environment almost the same weight of
3:06 all humans on Earth every year U and a lot of that goes into our water streams
3:12 so it comes kind of back to us all of the plastic almost all of the plastic is generated by fossil fuels so there are
3:19 emissions um implications to that um you know there is saying all waste is bad
3:26 bad in in an efficient organization we don't want waste plastic waste is especially
3:34 bad because it it just remains there you cannot get rid of it um so it's it it is
3:41 imperative for all of us to be able to drive as much of possible uh the
3:47 reduction in plastic use um and that's what we are going to talk about
3:53 today any any thoughts on the on the facts that I just mentioned it's incredible you I guess
4:00 the scale of the business is huge you know from from Juniper's side from the
4:06 amf1 side equally we are producing a lot of product relative to the you know to
4:12 to our end goal which is to to win a race and subsequently to win a world championship within within Formula One
4:18 um I I think from from my perspective we have although we have very different scales of challenge the fundamental core
4:25 principle of what we're trying to do is the same you know we are trying to reduce plastic waste trying to become
4:31 more sustainable businesses and and that for me I think is what we will'll explore shortly and and how much plastic
4:39 waste approximately amf1 is producing every year um that if if you have that
4:45 information so yeah what I have a slightly different uh a slightly different answer I guess um Ashley
4:51 because from our perspective we have we have so much varied waste whether it's composite waste resin waste um metallic
4:59 waste and and plastic waste so totally we produce about 361 tons of waste uh in
5:06 2023 this year we're on target to reduce that which is which which is great great news um of the 361 tons that we've
5:14 produced um 60% of it in the last 12 months was recycled and 36% of it was
5:21 recovered so so you know we are actively trying to you know improve our our
5:27 sustainability in this regard or our Waste Management and fundamentally that comes back to some of the benefits that we see both as
5:34 a society within amf1 and in the immediate surrounding areas within the UK oh that's very interesting um I mean
5:42 I I would give you an equivalent number from juniper side so we used 2022 which
5:48 is our Baseline year uh we used more than 1 million pounds of plastic in our
5:54 packaging alone so I'm discounting everything that we use in our operations or in the products just in packaging we
6:00 used more than a million pounds of plastic um we were able to reduce significant amount of it about 12% from
6:08 2022 to 2023 um about 130,000 pounds um probably
6:14 would be about maybe 70,000 you know kilograms I I would say or maybe 60,000
6:20 kilograms but if I all of these numbers you know don't mean much unless I I'm
6:27 able to visualize it right so we visualized it what is it in terms of you
6:32 know number of plastic bottles for example so1 130,000 is equivalent to a football
6:40 stadium filled with plastic bottles instead of people so that's the kind of the scale of plastic reduction and
6:47 plastic use that we're talking about within just our packaging and Juniper is
6:52 not a you know a huge company there are companies that are much bigger than us
6:58 so I want to emphas iiz to the audience kind of the scale of the issue that we are talking about um at hand um now
7:08 let's let's maybe talk about some of the drivers um can you can you speak to what
7:14 is driving eston Martin Formula 1 team to focus on waste especially plastic
7:20 waste and how you reduce it in your day-to-day operations yeah absolutely obviously for
7:27 the audience um as a business with in the UK we recognize and and are working towards the UK plastic pars targets so
7:35 that's our requirement uh driven um by the UK plastic pack um there are M
7:41 mainly there are four targets so we um Target one is to eliminate problematic
7:47 or unnecessary single-use plastic packaging and that's really how do we adjust how we operate design and
7:54 manufactur components uh to remove that waste the second Target then for us um
8:00 as part of the UK plastic pack is that um the 100% of our packaging that we use
8:06 needs to be reusable recyclable or compostable yeah now there are some simple things in that regard where even
8:14 uh in the factory itself with the 850 that I people I talked about earlier on
8:19 um at the moment we are using uh compostable cups for example uh as as part of coffee and and when in Formula 1
8:27 producing um you know such signific ific amounts of of parts per person uh coffee
8:32 is a very important product to the to the efficiency of the organization so we are using a lot of those cups at this
8:38 moment in time what we are about to do is is to issue a um a metallic cup
8:44 probably be an aluminium cup reusable cup and then remove that waste within our within our
8:49 organization and when we get to Target three we're then into 70% of plastic packaging effectively recyclable or
8:56 composted so in effect this is a slightly reduced um Target I think we
9:02 should actually aim for Target two and then Target four um is 30% of average
9:08 recycled content across all plastic packaging so they're the staged uh elements of the UK plastic PCT that's
9:14 our key um driver uh external influence from outside of the business I also
9:21 mentioned earlier on about internally we have our our um regulations that that
9:26 that basically um create the way that we operate as a Formula One team so whether
9:32 it's a technical regulation a sporting regulation Financial regulation or a sustainability or an environmental um
9:40 regulation from that perspective financially we are driven to continue to
9:46 take waste from our system plastic or anything else really which is a great way that um that the F and the
9:54 organizations as the teams are now coming together to work and understand how we can best utilize our common
10:02 understanding Comm common practices so they are the two perhaps One external factor and one internal Factor that's
10:08 driving our our our work in this area that's that's really interesting because
10:13 um I think for us as well the the activity really started with the EU
10:19 regulations around tax on single use plastic um we ship a lot of our product
10:24 to EU um and we do use uh signific ific amount of plastic in our packaging so it
10:31 would have you know resulted in increased cost for us to be able to ship that amount of plastic into EU um for
10:38 the benefit of the audience I I think we are going to be using three different types of plastics in in the discussion
10:45 so I want to clarify that for for everyone um single use plastic is
10:51 something that cannot be recycled so you use it and it goes into a landfill
10:56 basically there is really nothing you can do about it then you have have what I call Virgin plastic that could be a
11:03 single- use plastic or it could be plastic that can be recycled but virgin plastic means new plastic being created
11:10 from fossil fuel and then we have something called recycled plastic which
11:15 as the term implies you are recycling the older plastic to create uh new
11:21 plastic and it's in in terms of what is the worst single use plastic is the
11:27 worst virgin plastic is the next and recycled plastic is the best if you have
11:33 to use plastic you would like to use as much of the recycled plastic as uh possible so I was coming back to the
11:40 regulations part this is how we started on on our journey when we looked at the
11:45 upcoming regulations in EU especially in in Spain UK Italy um we realize that
11:52 it's going to cost us a lot if we don't you know change what we do and um and
11:59 then at at some level I feel like everybody is an environmental Steward right and
12:05 you know all the employees our customers our stakeholders they would all like to
12:11 do the right thing so once the regulations move us in in a certain direction it picks up momentum and then
12:18 you you know work on it work on it and you reduce um the amount of plastic that you're using in whichever operations or
12:25 uh your product uh we talking about and it's interesting I think I also want to touch on the um the cups the compostable
12:34 cups that that you talked about um one of our employees or or several of our employees highlighted the amount of you
12:42 know plastic bottles or the number of plastic bottles we were using um in meetings uh in our cafeteria as well as
12:50 these twoo boxes that that people use to take food home or take food to their uh
12:56 desk rather than eating uh onsite and we were using plastic for both of those so
13:01 our our teams worked on getting rid of both of those activities you know we have non-plastic basically uh utensils
13:09 that we are using but I like that idea of metallic cups um you know that will be something that uh that sounds
13:15 interesting so I'll keep in touch with you on on how that goes and we hopefully we Implement that on our side as well um
13:23 so now let's move on to um the
13:29 um the actions that that you're taking uh related to this do you differentiate between virgin plastic versus recycled
13:38 plastic I'm not talking about you know recyclable plastic but do you guys have any any thoughts around I want to use as
13:45 much recycled plastic as possible yeah it's an interesting question ashle you I
13:51 guess where where we where we are um as a Formula One team we have high
13:56 development you know we we touched on earlier through the year if we um
14:02 structure part numbers required to build a car we may see more than 20,000
14:07 released Parts yet with small batch quantities so so we're in a very very
14:13 fast turnaround highly bespoke you know development organization and I think from my
14:21 perspective what we see here is a real challenge because while we we still have
14:26 to consider our contribution to the trade back we should also consider you know how contribution to to the to the
14:33 to the planet you you mentioned we're all stewards of the environment y now
14:39 where we are um where we are operating within Formula 1 we use a lot of um SLA
14:46 so they they they are basically 3D printed Plastics um typically we'll be we'll be
14:52 we'll be virgin Plastics or single-use Plastics um we do not differentiate between the two however what we do
14:59 recognize is that when we produce the components there is also a lot of waste within the manufacturing process of
15:05 which some is 90% plus wasted resin material okay now again we as a Formula
15:13 One team we're driven by the innovation of how we improve this process how do we make it more uh efficient and how do we
15:20 take more product from the investment that we've made now while we do that we have done a
15:27 hell of a lot of work in understanding how we can turn the utilization of that
15:33 raw material um into more finished product in effect becoming more
15:39 sustainable and at that point what we realized is that where we have low yield currently you know nine or 10% similar
15:46 to some of the plastic usage were talking about earlier on we actually um are able now to recycle or reuse the
15:53 resin yeah with through a a process that we've set up with the supply chain so
15:59 effect where we lose the material and we don't take the yield of the raw material the resin will be returned and recycled
16:05 and we reproduce parts from the same batch so from our perspective that's a real big step forward um within our
16:13 additive manufacturing world where we can now start to improve our recycling
16:19 of the raw material to improve our um reduction strategies or our our process
16:25 within reducing waste but also allows us to produce more product from that same raw material so it helps us with our
16:32 with our increased throughput yeah that's that's again very interesting I think that is a there's a
16:38 slight what I call the difference in the business model um your company is its
16:44 own customer right so for us it it is we ship these products to customers and
16:51 then there is very little opportunity for Juniper um itself to be able to reuse
16:57 that plastic or recycle it uh or get it back and in that sense um you know the
17:03 stakeholder involvement becomes a pretty big deal um so if if our customers um
17:10 request for example us to uh become more sustainable there is a very big
17:15 contribution from them uh to be able to do some of those things that you talked about on site when they are you know
17:22 taking the packaging off of the uh product and and I think that's probably
17:27 the the reason why we we are emphasizing primarily on moving a
17:33 lot of the plastic used to recycled plastic as much as possible um because
17:39 of that reason because we don't know what happens to that plastic once it gets to our customers locations um it
17:46 might get discarded it might get recycled or not so we want to minimize the you know the footprint from ours
17:52 point of view and that requires us to minimize the um use of Virgin plastic in
17:57 our uh Packaging um that brings me to a very interesting um Point here around
18:05 challenges what challenges do you see um on this journey as well as some of the
18:12 activities that you are you are taking up to reduce uh waste to reduce plastic
18:18 waste especially uh within the organization yeah absolutely I I mean
18:23 there are a couple of things within the organization you touched on ash there a very good point that we are we are our
18:29 own supplier and customer so so in internally we we are in complete control
18:34 of of what we do now um from our perspective that is that is a great
18:40 opportunity to make a real difference within the organization um but I think that the core the core driver behind it
18:46 is an understanding of everybody that is within the organization and and the surrounding areas within the supply
18:52 chain to really understand why are we doing this yeah why are we trying to reduce waste particularly plastic waste
18:59 why are we trying to become more sustainable and as part of our journey um along that
19:05 um along that road what we've decided is that we have implemented a um a
19:11 management system if you will that is um is linked to a British standard it's a it's an an ISO standard it's 14,000 And1
19:19 and in effect what that drives us to do um and it is a mandate of the standard
19:25 is to make sure that we measure so at least we have a data set by which we can refer which is you know I touched on
19:31 earlier on the total waste produced in 2023 this really starts to keep us
19:36 honest and aware of of of what it is that we are producing and creating I think that's I think that for me is the
19:43 first challenge yeah once you understand the scale then you can start to transact and action some of the the response and
19:51 um counter measure uh strategies that that we need to do to to continue to
19:56 push sustainability Beyond beyond that um management system we also make sure that
20:03 if we see variants to our targets that we're very open with the team yeah we we've got to make sure that people are
20:10 completely empowered and informed with where we are performing against our our
20:15 targets so I gave you the example of additive manufacturing and trying to
20:20 improve the use of the of the raw material we also um we also are in a
20:26 position where we are trying to take um what cannot be reused so where we have product that's being raw material
20:33 that's being utilized in the building that cannot be reused what else can we do with it yeah so we have seek uh seek
20:40 to find uh globally some opportunities where we can use um the raw material as
20:48 a back fill or filling uh system for roadways for example so we're currently
20:53 going through some analysis to see whether we could reuse the Raw material
20:59 rather than recycling our own world it's not as you know it's not as beneficial but at least it's a step forward for us
21:05 in that regard now the challenge comes and I think some of the questions may may push us in this direction where we
21:13 continue to develop race after race obviously we create more and more um
21:18 waste and we are using more and more raw material so the the simple question is
21:24 well for the more that you produce Ben the more waste that's created what do you do with more waste and that's where
21:30 the teams you know uh month on month we see the waste increasing we then have to start to offset with our reuse or
21:37 recycle strategies and I think Ashu there the two challenges yeah it's having our uh having our management
21:44 system making sure that we are honest open and aware of our our
21:49 contribution and then beyond that where we Implement strategies to try and manage the variances and our targets
21:56 that's just keeping the team engaged and empowered to make to make sure that we can
22:01 achieve yeah I mean I think that that's again you know that's a basic tenant of
22:07 of improvement right if you don't measure you cannot improve right the the
22:13 first thing you need is the is the baselining or the measurement of what what you currently have and I think
22:19 that's you're absolutely right that's a that's a challenge um to do especially
22:25 um for something as diverse as use of plastic you know you it it's everywhere in in your in your offices in your
22:33 cafeteria in your operations in your packaging in your product so getting all
22:39 of that together to get like an organizational level of uh plastic consumption is is pretty hard um and I I
22:46 think I want to probably speak a little bit around the challenges that um that
22:52 Juniper has from a from a scalability point of view I I think that's that's
22:57 the basic difference between the organizations right it's a it's a high volume manufacturing versus um PE spoke
23:05 but very precise manufacturing um that amf1 uh has for for us you know some of
23:11 the challenges are pretty obvious as I mentioned in the beginning um only about 9% of the total plastic that gets
23:18 produced every year is recycled and that leads to issues with Supply we just
23:25 don't have enough supply of recycled plastic uh and if there is Supply it comes at a
23:32 slight premium to using Virgin plastic and Plastics are you know incredible
23:38 from that point of view it's one of those Commodities I would say where a
23:45 recycled part is more expensive than a new part it's it's cheaper to create new
23:51 plastic than it is uh to create uh recycled plastic it's you know just in
23:57 in that that is amazing to us so what that leads to is some cost premium um on
24:04 the most parts that we want to move to recycle plastic from Virgin plastic as
24:09 well as the risk to supply because then a lot of our packaging materials are locally sourced so wherever our
24:16 manufacturing factories are and there are several uh in order to reduce risk to supply chain we have to go to local
24:23 suppliers and and get the recycled plastic packaging parts and that's
24:29 that's challenging that has been uh that has proven hard to to do and then one
24:35 very interesting challenge that we also see in in our overall
24:40 sustainability you know um world view our carbon emissions
24:46 are are as important of a metric to us as reduction in plastic and what ends up
24:54 happening is when you try to go to non-plastic Packaging or even recycled
25:00 plastic packaging generally the size and the weight of the component is bigger so
25:07 it's it's a bigger volume it's a bigger weight to get you the same cushioning
25:13 you know that you need to protect your product and you know at the end of the day packaging is is functioning as as
25:20 protection while your product is in shipment so by using heavier bigger
25:27 pieces that are non-plastic or recycled plastic you increase your Logistics
25:32 emissions so then it becomes a a game of balancing increase in logistics
25:38 emissions with the desire of reducing virgin plastic use in in your packaging
25:45 and we have developed certain models that we we rely on to see how much is
25:50 the increase in emissions and how much is the um you know reduction in plastic and so on and we make decisions that way
25:57 but I I would come back to a point I made initially some of that is dependent
26:03 on what our customers want so for example if our customers agree to using
26:11 ocean shipment for their products which of course has a increased lead time it's
26:16 much easier for us to use non-plastic packaging or recycled plastic packaging versus virgin plastic so there is
26:24 there's significant amount of stakeholder involvement customer involvement and engagement that's
26:30 required for us to make that transition to non-plastic or recycled plastic um
26:36 packaging if you want to get there you know 100% um so I I found that you know
26:43 through this activity I found that to be um the case and and I was again very
26:49 surprised the balance between the emissions versus you know plastic reduction it's it's not one any all so
26:56 you have to you know keep just like everything else I guess uh you have to make a balance between the
27:02 two um so let me just touch on um something related to emissions as
27:10 well I know Formula 1 has um very stiff targets to become Net Zero
27:16 I believe it's Net Zero by 2030 and I'm sure you know they are pushing on individual teams to you know get there
27:23 as well do you guys have any any you know specific activities or plan plans that you are doing for reducing carbon
27:30 emissions within your organization as well yeah obviously as you we we touched
27:36 on earlier on we we we have a global sport yeah 24 races a year all across
27:41 the globe so naturally that becomes challenging with regards to carbon emissions because we we constantly move
27:49 product around the globe from race to race now when we do that our key driver is
27:56 the more product that we put into a SE Freight Transportation Route rather than
28:02 Air Freight the lower the carbon contribution so that's one of our primary drivers at this moment in time
28:08 is how can we minimize Air Freight and maximize SE Freight as as a you know as
28:15 a big step forward um but but in addition to that what we also should consider is as a
28:22 group of of F1 teams a group of 10 teams we we now come together uh on a routine
28:29 basis with the FIA um to discuss and understand where we are as a team on our
28:35 journey to to Net Zero 2030 and within that environment there
28:40 is more and more common ground and understanding being developed so I think you know strategically as teams although
28:46 we're not quite there yet the the the desire and and and focus is now heading
28:52 towards 2030 at Net Zero and as the teams come together obviously the more
28:58 the more input and the more alignment that we have the more effective our journey is uh in that direction so so
29:05 there there're the two I say they're the two priorities at this moment in time um
29:10 beyond beyond that really um it's it's everything that we do as as part of our uh carbon road map so um so so we can
29:18 probably discuss that in far more detail in the future I'm sure and and I'm sure you know for for
29:25 you I mean it is for us the engagement from all of our employee base all of our
29:31 leaders in the organization um we all have to go there as one right unless you
29:38 have enthusiasm unless you have um that drive from your own organizations these
29:44 things are are really hard to to achieve so what do you guys do to um encourage
29:50 excitement within amf1 towards sustainability towards waste reduction towards emissions reductions and and so
29:56 on yeah yeah it's a really good it's a really good question Ashu and as as we touched on earlier on um it's a it's a
30:03 big challenge you know the the education peace is is a huge is a huge part of of
30:10 what we we owe to ourselves as as um stewards of of the environment but also
30:15 to to our employees and our supply chain so from our perspective um we try to um
30:22 to bring employees together in things like sustainability day so we created a day on the center of the factory um or
30:29 the center of the campus we set up maybe 15 or 20 stalls of all different types
30:36 of small businesses that have workshops on beeswax and how we can reuse it on
30:42 how we manage waste uh through recycling how we can as human beings make a better
30:48 contribution to to the environment and to our waste um by changing simple things day and day out the obvious one
30:55 that came out of that Forum or that that event was the the you know the coffee cups that we we touched on earlier on
31:01 and by by bringing people in to an environment that is still in the workplace but is completely separate and
31:09 completely isolated away from the general day-to-day work it drives to it drives some energy within within the
31:14 organization because it now becomes real yeah we can now see um a large
31:20 proportion of the the the staff that we have within the team engaging with that um that exciting environment on the on
31:26 the ground floor of the campus so that was a huge step forward for us what we also do is we have a routine
31:33 exec sponsored um sustainability um steering committee that ensures that
31:38 where we have opportunities and where we have improvements and and the the supply chain and the internal um the internal
31:46 employees come up with ideas of how we can improve there is a place for it to go as a suggestion so that we can then
31:52 put adequate resource and empowerment behind it so between you know between type of um
31:59 you know highly engaging firsthand experience with Specialists within the sustainability
32:06 Arena as well as having a a mechanistic you know uh Cadence within the the me
32:11 the organization that's how we've continue to drive the engagement and the excitement within the building yeah very
32:18 very interesting and and I think I have to say um fairly similar to the the
32:23 structure that we are adopting right I I think um much of this flows from top
32:30 down so you have to have um your leaders you know driving the importance of this
32:38 into the rest of the organization and for that purpose we we have you know incentives already um we we use
32:45 something called an okr process um we have an okr at the at the executive level where we you know sustainability
32:52 is front and center and that that kind of flows through to the rest of the organization
32:58 uh we have also created uh some employee experience pillars and one of which is
33:04 uh sustainability and again the objective is exactly the same to get ideas from the general employees um as
33:12 well as you know bit more crowdsourcing uh bit more communication on things that
33:17 we're doing well already um it's U the the motivation if you're already doing
33:23 well is far better than uh if people don't know about it so that's kind of
33:29 the other other thing that we do uh to create excitement within within our employees um at at this point Ben I
33:37 would want to transition um into maybe let's take an uh an audience question or
33:43 two if you don't mind absolutely let's do that okay so let me read the first
33:48 question that we received from our audience um can you provide more details
33:53 on the progress Juniper has made in reducing PL Plastics um so as I was mentioning in
34:01 the beginning we baselined our our plastic use just in our packaging for 2022 and
34:08 it was more than a million uh pounds of plastic that we were using um
34:14 approximately I would say about 25% of that was virgin plastic so you know
34:21 somewhere around 250,000 pounds of orgin plastic so from 2022 to 2023
34:28 we reduced our virgin plastic use by 45% in just one year again focusing on the
34:36 high volume parts that were contributing the most virgin plastic and trying to move those to recycled plastic material
34:42 as as much as possible or to non-plastic materials so we are we are trying to
34:47 move a lot of our packaging to um single type compostable which is what our
34:52 customers want as well and our customers have been have been really helpful in
34:58 you know making us get there um so we reduce our virgin plastic by 45% and our
35:03 overall plastic use by 12% just in one year from 2022 to
35:08 2023 um our targets are really ambitious I don't know if we are going to meet or
35:14 beat all of those targets but we're going to do our best so we want to reduce the overall plastic by
35:22 40% by next year by 2025 and again it's a very challenging goal
35:28 within that we want to reduce the Virgin plastic part of it to less than 15% of
35:35 the overall plastic and remember it was about 25% in 2022 so very ambitious
35:41 goals Juniper has I think we' have made very good progress um over 2022 23 uh
35:48 but you know every leg lower becomes more challenging uh but we we are on our
35:53 way um then I'll take one more questions um apart from actions Juniper and amf1
36:02 is already taking what are some effective ways organizations can
36:07 contribute to reducing plastic waste in their operations and supply chain um Ben
36:13 I I'll I'll come to you on this any any thoughts uh you want to provide on that one yeah I think we touched on a couple
36:20 of times ium regarding the supply chain so where we recognize high impact
36:26 suppliers yeah it's really for us to develop the relationship with the suppliers and continue to mature through
36:33 our um through our Target setting that they are included within this we touched
36:38 I saw 14,000 And1 earlier on where we are managing our data sets managing our
36:43 targets and empowering our our internal employees and staff to achieve them when
36:49 we go external within the supply chain we work in a very similar way yeah so where we continue to raise the awareness
36:56 with the supply chain we also expect the same commitment and drive forward so that's part of my
37:02 responsibility to encourage that um that that maurity within the supply chain beyond that when we think about um we
37:11 think about internal staff we've spoken about engagement exitement I think you mentioned about continuing the
37:16 communication I think that's keeping it front and center is really key within the organization whether it's in uh live
37:23 displays whether it's in you know leaflets that go within the within within the the building whether it's
37:28 online wherever we can we can we can publish this information we we should
37:33 and we do um and beyond that then really we at a at a very you know at a very simple level I guess we um we can take
37:42 some small examples um where internally um we use um uh some packaging at times
37:50 within the factory to protect Parts yeah because we we don't want parts to to be
37:55 to Decay during the manufact in process now where possible we've looked to reduce that that that plastic
38:03 waste either by reuse or um actually replacing it with a a better alternative
38:10 so um we now use a um a very simple cardboard or paper equivalent to the the
38:18 plastic the plastic use that we've seen previously so I think they are the three stages really of of an external supply
38:24 chain the internal manufacturing operation but also uh making sure that
38:29 the staff are continually uh communicating and and understanding of where we're at within our within our
38:35 Target setting and making sure that the supply chain follows our in our footsteps yeah absolutely and and I I
38:42 think pretty much the echo the points that that you made um the only thing I
38:48 would I would say is sometimes as far as your own
38:54 organization your own employees are concerned small things make a big difference right and and I gave the
39:01 example of um eliminating plastic bottles and and to go containers in the
39:07 cafeteria even though the absolute plastic reduction from that activity is probably not that much you know we we
39:13 probably reduce a lot more by just converting one packaging part to
39:19 non-plastic um but the Optics of doing that um the motivation it brings to our
39:25 employee base um as well as the enthusiasm it it brings is invaluable so
39:31 you have to look at you know small impact but big Optics type of activities
39:39 um as well not only you know what is what is the high volume activity from
39:44 from our point of view as well and I I heard you say beeswax somewhere in in
39:50 there um can you can you speak to what what that is that's very interesting to me yes so uh what we we had a um a
39:59 specialist um company come and join us where they were using beeswax to wrap
40:07 and and and basically secure or protect product yeah so that's you know I guess
40:13 it's it's almost like a natural reuse um uh solution so they joined us on our
40:20 sustainability day and just explain to the uh to the staff to the employees and the attendees to the event how we could
40:27 would utilize beeswax you know in in our lives really um and it's great because
40:33 when you see the ideas and and and promote this you know this engagement
40:39 the impact that it has on the employees or the the people engaging with it as you just touched on it makes a huge
40:45 difference um you know within the culture of the organization and within the thinking of the of the people that
40:50 are engaged with it allbe it that the contribution to the you know to our Global goal or our stewardship of the en
40:57 environment as as you suggest is perhaps negligible yeah and and those those are
41:02 a really interesting really interesting steps I think we linked to that we also
41:08 um you know we must avoid um based on um what the UK requirements are that um
41:13 disposable CL PL plastic Cutlery just doesn't exist as a thing for us anymore you know we we now have various
41:21 different types what we try to do is is is allow people enough um
41:27 uh product available to them in the in the Cen or the rest areas so that we continually rewash you know metallic um
41:35 equivalents so a little bit like the the the metallic coffee cup that each employee will will have we also do the
41:42 same with with the cuty within within the Cen so so they are the small you know the small gains but huge Optics
41:48 that that you touch on just now yeah wonderful so Ben we we're coming um on
41:54 on time uh I I really want to thank you you for joining me uh in this chat today
42:00 and all the valuable insights that you provided not only to me but to our audience uh as well thank you very much
42:06 ben no problem it was a pleasure [Music]